How COVID Impacted Custom Home Builders
COVID had a devastating impact on home builders
Great construction projects come from great planning, and from choreographing a dizzying array of thousands of people, products and processes. That planning and choreography were rendered impossible by COVID and the world’s policy responses to the virus.
Here is how our operations team summarized the various challenges encountered across different phases of construction and with different materials and trades. These challenges include delays in obtaining permits, utility connections, escalating material costs, labor shortages, and disruptions in supply chains due to various factors such as natural disasters and pandemic-related issues. The most impactful disruptions for Turnstone and our clients were in the area of cabinetry since most of our Pennsylvania-based suppliers were shut down.
Each section outlines specific issues faced within different categories such as concrete, steel, framing, trusses, insulation, roofing, exterior finishes, windows, appliances, cabinets, HVAC, and electrical work. The delays and cost increases mentioned underscore the widespread impact these challenges had on the construction process, affecting timelines, costs, and overall project management. Further, these issues were interconnected, where delays in one area rippled through and impacted other aspects of the construction project. This comprehensive overview provides valuable insights into the complexities and challenges Turnstone faced during this period.
General Conditions
- Missed Employee Time/Remote Working: Remote work and absences affected our team, trade partners, and suppliers.
- Project Manager Burnout - PMs faced long hours and incredible stress with no predictability regarding the items detailed below.
Permits
- County and Municipal Permits: Permitting times increased significantly. Standard wait times were 3-4 months in Rehoboth and 6 weeks for county reviews, with some permits taking up to 5 months.
Utilities
- Sewer/Water/Electrical Connections: Connections faced severe and unpredictable delays.
Concrete
- Price Increases: Prices have steadily risen due to increases in steel and labor costs since the beginning of COVID-19.
Steel
- Price Increases: Similar price increases due to steel and labor costs.
Framing
- Material and Labor Costs: Costs for framing materials increased by over 400%. The labor pool was also affected.
Trusses
- Price Increases: Truss prices rose by 80-100% due to material costs.
Stair and Railing
- Lumber Price Increases: All lumber items were impacted by the rising lumber index.
Interior Trim
- Lumber Price Increases: Similarly affected by the rising lumber index.
Gutters
- Aluminum Price Increases: Prices increased significantly, partially due to hurricanes in Florida.
Insulation
- Availability and Cost Issues: Insulation was nearly unavailable and costly due to two chemical plant destructions in Texas.
Roofing
- Product Availability and Price Increases: Limited production led to sharp price increases, especially for metal roofing.
Exterior Finishes
- Material Shortages: Plants running on limited capacity caused shortages and price increases in wood siding, aluminum, vinyl, and PVC products.
Windows
- Lead Times and Price Increases: Limited operating capacity led to long lead times (up to 12 months) for some Andersen window products.
Garage Doors
- Lead Times: Expected lead times extended to 12 months.
Wood Flooring
- Price and Manpower Issues: Prices increased moderately, but manpower was significantly affected.
Painting
- Scarcity and Price Increases: Occasional scarcity led to price increases.
Appliances
- Availability and Delivery Issues: Plant shutdowns, material shortages, and shipping challenges made availability and delivery dates totally unpredictable. Builders were hoarding cheap appliances to put in homes in order to get certificates of occupancy.
Cabinets
- Our biggest challenge - Production, Quality Control and Cost Issues: Pennsylvania cabinet factory shutdowns caused production delays and cost increases. When cabinets eventually shipped, they often arrived damaged or not as ordered. Which meant the whole cycle had to start over.
HVAC
- Equipment Shortages: Sporadic shortages of certain condensers were unpredictable.
Electric
- Supply Issues: Monthly shortages and indefinite backorders affected wire, devices, panels, buses, and breakers, causing massive delays.
Any delay in one trade partner's work impacted all other areas of the project.
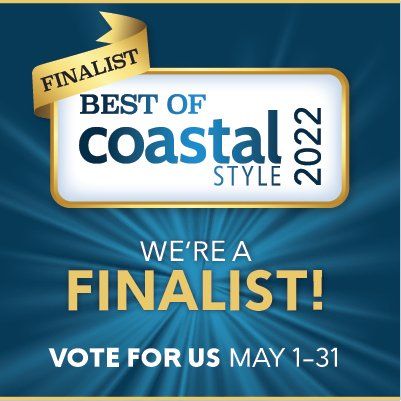
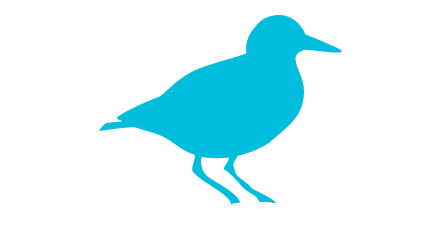
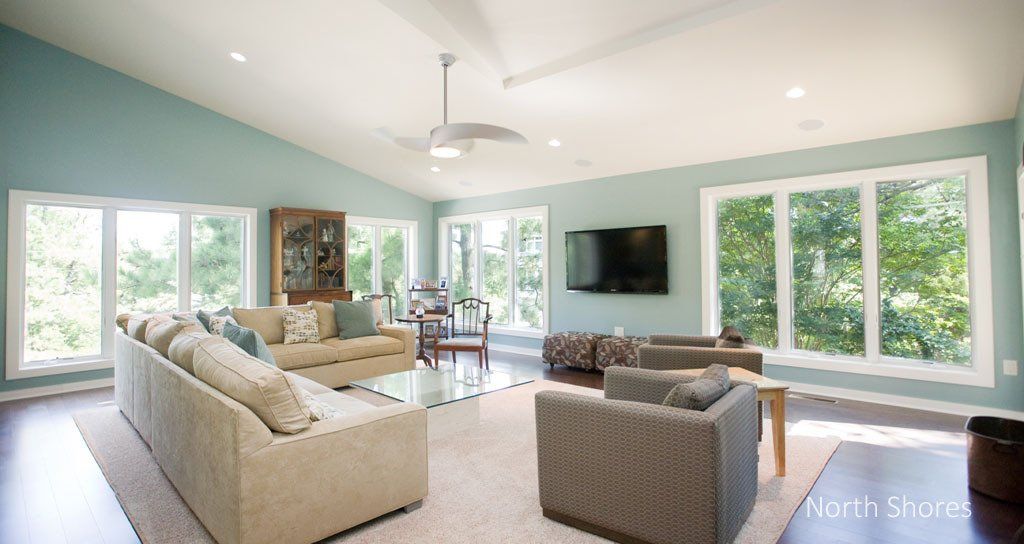
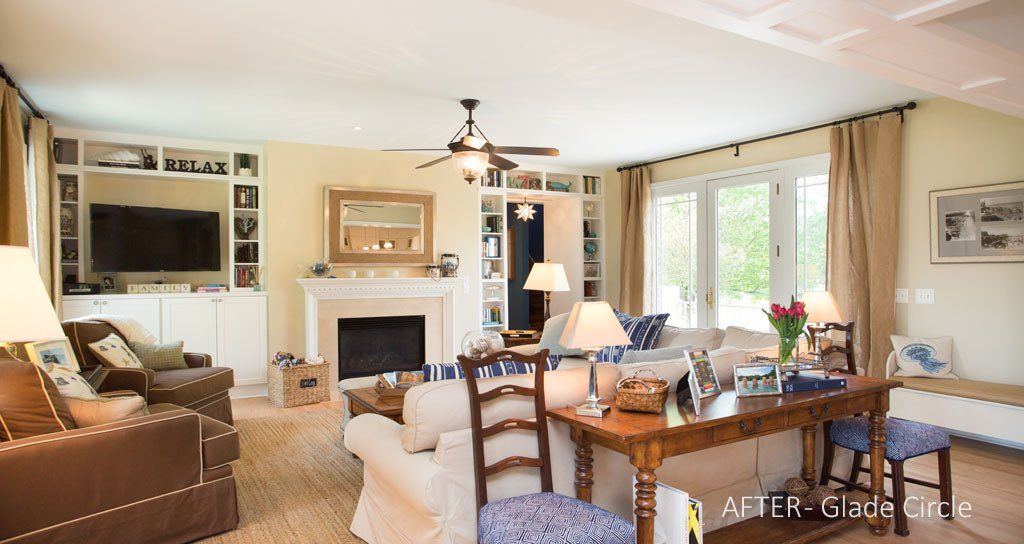